分享到微信朋友圈x
打开微信,点击底部的“发现”,
使用“扫一扫”即可将网页分享至朋友圈。
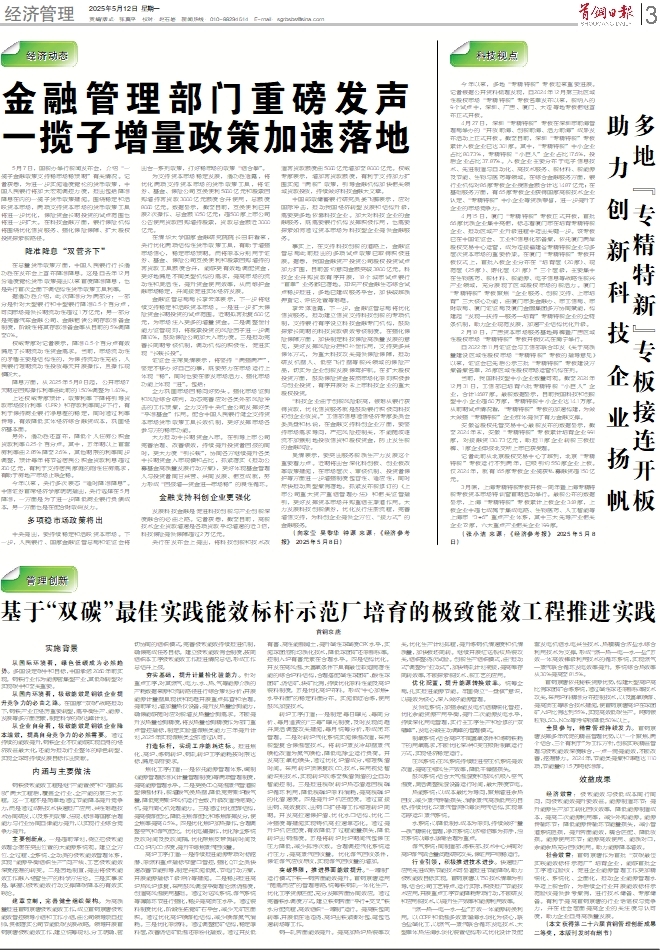
- 返回目录
- 上一篇
- 下一篇
- 放大+
- 缩小-
- 常规
基于“双碳”最佳实践能效标杆示范厂培育的极致能效工程推进实践
实施背景
从国际环境看,绿色低碳成为必然趋势。多国设定碳中和目标,中国承诺2060年前实现。钢铁行业作为能源密集型产业,其低碳转型对实现碳中和至关重要。
从国内环境看,极致能效是钢铁企业提升竞争力的必由之路。在国家“双碳”战略推动下,钢铁产业正经历重要转型,需平衡生产、能源、发展等多方面因素,制定科学的碳达峰计划。
从企业自身看,极致能效是钢铁企业降本增效,提高自身竞争力的必然需要。通过持续的能效提升,钢铁企业不仅能够实现自身的经济效益最大化,还能为推动行业整体的绿色转型、实现全球可持续发展目标作出贡献。
内涵与主要做法
钢铁极致能效工程是继“产能置换”和“超低排放”两大工程后,覆盖全行业、全产能的第三大工程。这一工程不是简单地通过节能降本提升竞争力,而是通过成熟技术快速推广应用、共性难题技术协同研发,以及系列政策、法规、标准等国家治理能力与行业协同自律能力提升,以实现行业综合竞争力提升。
主要创新点。一是超前谋划,树立把极致能效理念摆在突出位置的大能源系统观。建立全方位、全过程、全系统、全动员的极致能效管理体系,实现“能源平衡组织生产”向产线、工艺极致能效深度挖掘的转变。二是因地制宜,提出将极致能效工作融入经营生产的科学方法论。三是实事求是,掌握以极致能效行动支撑降碳降本的有效实践论。
建章立制,完善健全组织架构。为高质量推进首钢京唐极致能效工作,成立首钢京唐极致能效管控领导小组和工作小组,由公司领导亲自挂帅,贯彻落实公司节能低碳发展战略。领导开展首钢京唐极致能效工作,建立统筹规划、分工明确、密切协同的组织模式,完善极致能效持续推进机制,确保完成任务目标。建立极致能效例会制度,按周组织本工序极致能效工作推进情况总结,形成工作总结并上报。
夯实基础,提升计量检化验能力。针对重点工序,对其燃气、电力、水、热、气等能源介质的产耗数据来源和流转路径进行综合策划分析;开展能源计量器具现状和问题开展重点排查和治理。提前谋划,增加量热仪设备,提升发热量检测能力,确保能够随时应对新增发热量检测需求。不断提升发热量检测精度,将发热量检测精度作为部门重点管控指标,制定实验室煤焦类能力三年提升计划,2025年实现煤焦类全部通过认可。
打造标杆,实现工序能耗达标。推进焦化、高炉、炼钢转炉、钢轧转炉工序能耗按时限达标,满足政府要求。
焦化工序打造:一是依托能源管理体系,编制《能源管理标准》《计量管理制度》等两项管理制度,提高能源管理水平。二是更换CDQ高温蒸汽管道新型保温材料,新增酸气换热器,降低克劳斯炉酸气量,降低克劳斯炉风机运行台数,升级改造污泥离心机,提升离心机处理能力。三是通过优化配煤结构,提高瘦煤配比,降低主焦煤配比和炼焦煤挥发分,使全焦率提高0.5%。四是优化焦炉加热操作,合理调整空气和煤气配比。优化电捕操作,优化除尘系统反吹时间及反吹间隔,优化筛焦皮带倒转时间及CDQ炉内CO浓度,提升干熄焦蒸汽回收量。
高炉工序打造:一是持续推进能源专项对标挖潜、原燃料重点指标窄窗口管控,强化QTI全员快速改善节能引导,制定并实施低氮、节电行动方案,开展能源指标T级评价等措施。二是稳步推进高炉热风炉修复,采用鼓风调湿平衡理论燃烧温度,创造高风温使用基础。通过对送风系统、煤气系统等薄弱环节进行强化,稳步提高顶压水平。通过装料制度优化,阶段性拓宽矿石平台,减少无矿区面积。通过优化高炉喷煤枪结构,减少喷煤氮气消耗。三是优化原燃料。通过调整配矿结构,稳定厚料层,改善烧结矿低温还原粉化指数。通过开发低有害、高性能膨润土,提升碱性球碱度CPK水平,实施球团溶剂均质化技术,降低球团矿还原膨胀率。控制入炉有害元素在合理水平。四是结构优化。开发在高风温、大富氧条件下具有最佳软熔滴落性能的综合炉料结构,合理搭配碱性球团矿、酸性球团矿、烧结矿、块矿比例,持续优化原料性能及高炉装料制度。五是优化高炉布料。形成“中心加焦+水平料面”的稳定料面分布。实施低硅冶炼,使用鼓风加湿技术。
转炉工序打造:一是制定每日曝光、每周分析、每月追责的“三每”曝光制度,及时发现问题并灵活调整攻关措施,每月统筹分析,形成闭环管理。二是对转炉汽化系统实施保温改造,采用新型复合保温层技术。将转炉蒸发冷却器蒸汽喷枪改造为氮气喷枪,降低电除尘运行负荷。开发高压氧枪喷头,通过优化炉渣成分,缩短溅渣时间。采用转炉顶底复吹CO2技术,采用视觉智能识别技术,实现转炉吹炼至溅渣倒渣的全自动智能控制。三是推进脱碳转炉热态渣返回脱磷炉循环利用,降低脱磷炉原料消耗,提高脱磷炉的化渣速度。四是提升炉机匹配度。通过直接出钢、高效复吹、出钢口扩径等工作缩短转炉周期。开发高拉速保护渣、优化水口结构、优化二冷强度等措施实现铸机高拉速常态化。通过提升炉机匹配度,有效降低了过程能量损失,降低转炉出钢温度。五是将转炉封炉期间汽包保压压力降低,减少排污次数。合理调控汽化系统运行压力,提高蒸汽回收量。优化煤气回收条件,保证煤气应收尽收,实现煤气回收量的增加。
突破界限,推进界面能效提升。“一罐制”运行模式下铁—钢界面能效提升。首钢京唐运用“随需而应”的管理思路,统筹铁钢轧一体化生产,优化工序资源匹配,充分发挥界面协同效应。通过完善铁水调度方式,建立铁钢界面“平行+交叉”铁水分配流程,高效组织“一罐制”运行。提高铁包周转率,开展低在途连浇、高炉出铁紧凑对包、尾包迅速转场等工作。
钢—轧界面能效提升。提高加热炉热装率攻关,优化生产计划排程,提升炼钢机清速度和机清质量,加快板坯周转。继续开展红送裂纹热装攻关,组织整浇次试验。创新生产组织模式,由“推动式”调整为“拉动式”,加快铸轧计划衔接,提高库存周转效率,不断探索新技术、新工艺的应用。
优化配置,提升能源转换效率。统筹全局,扎实推进能源节能。牢固树立“一盘棋”意识,以提效为核心,深入做好能源管理。
发供电系统:加强余能发电机组精细化管控,优化余能资源产用平衡,提升二次能源发电水平,持续深化用电管理,实行主工序生产和检修的“双错峰”,发电谷段主动调峰的管理模式。
制氧系统:结合高炉不同富氧条件和炼钢铁耗下的用氧需求,不断优化深冷和变压吸附制氧运行方式,实现经济稳定运行。
压风系统:压风系统持续推进空压机系统提效改造,提高压缩风生产效率,降低干燥器损失。
鼓风系统:结合大气温湿度和鼓风机吸入空气温度,灵活调整脱湿设备运行时间,最大限度节电。
热能系统:以成本最优为导向,聚焦增进余热回收、减少蒸汽传输损失、消除蒸汽高质低用的目标,持续优化S2蒸汽管网和海淡用汽结构,实现常态停运S1蒸汽系统。
水系统:以降低制水成本为原则,持续做好“量—质”精细化管理,净环系统以浓缩倍率为抓手,浊环系统以海水渗漏治理为重点。
煤气系统:同制造部、炼铁部、技术中心共同对高炉煤气硫含量问题研究攻关,保证用户顺稳运行。
行业引领,积极推进技术进步。快速推广应用先进成熟节能技术可显著推进节能降碳,助力极致能效目标实现。首钢京唐以T50技术清单为引导,结合公司工艺特点、运行实际,积极推广节能技术应用,开展重点工序节能降耗专项行动,不断研发和应用新技术,以提升生产效率和能源利用效率。
“燃—热—电—水—盐”五效一体能源转换利用。以CCPP和低温多效蒸馏海水淡化为核心,联合盐碱化工,以燃气—蒸汽联合循环发电技术、大型单体热法海水淡化装置结构形式优化设计及配套发电机组水电共生技术、热膜耦合浓盐水综合利用技术为支撑,形成“燃—热—电—水—盐”五效一体高效梯级利用技术的循环系统,实现燃气—蒸汽联合循环发电效率提升。系统综合热效率从30%提高至81.5%。
首钢京唐依托秘铁资源优势,构建大型高炉高比例球团矿冶炼系统,通过碱性球还原膨胀率技术攻关,采用炉料精准分布控制技术,以及富氧喷煤、提高顶压等综合技术措施,使首钢京唐高炉在球团矿入炉比例达到55%,实现高效低碳生产。吨钢颗粒物、SO2、NOx等污染物降低50%以上。
全员参与,精益管理持续发力。首钢京唐发挥多年沉淀的精益管理优势,以“一个聚焦、两个结合、三个有利于”为工作方针,创新实践精益管理与极致能效深度融合,一点一滴提能效,不断改善,挖掘潜力。2024年,节能类提案和课题达1110项,节能量约1.5万吨标准煤。
效益成果
经济效益:极致能效与极低成本同行同向,向极致能效提升要效益。能源制造环节:提升能源生产加工转化回收效率,降低能源制造成本,提高二次能源利用率,减少外购能源。能源传输环节:降低能源传输环节能量损失,减小管道系统阻损,提升界面能效,耦合匹配、降低放损。能源使用环节:能源高效使用、能质对口,余能余热充分回收利用。助力能源降本增效。
社会效益:首钢京唐作为首批“双碳最佳实践能效标杆示范厂”培育企业,能够首批全工序通过验收,促进企业能源管理工作更加精细化、系统化、全面化,推动企业能源管理水平迈上新台阶,为后续全行业开展能效标杆示范验收提供参考案例,进行技术储备、专家储备。有利于提高首钢京唐的行业话语权与竞争力,并在社会层面提高企业的关注度与认可度,助力企业自身高质量发展。(本文获得第二十六届首钢管理创新成果二等奖,本版刊发时有删节)