分享到微信朋友圈x
打开微信,点击底部的“发现”,
使用“扫一扫”即可将网页分享至朋友圈。
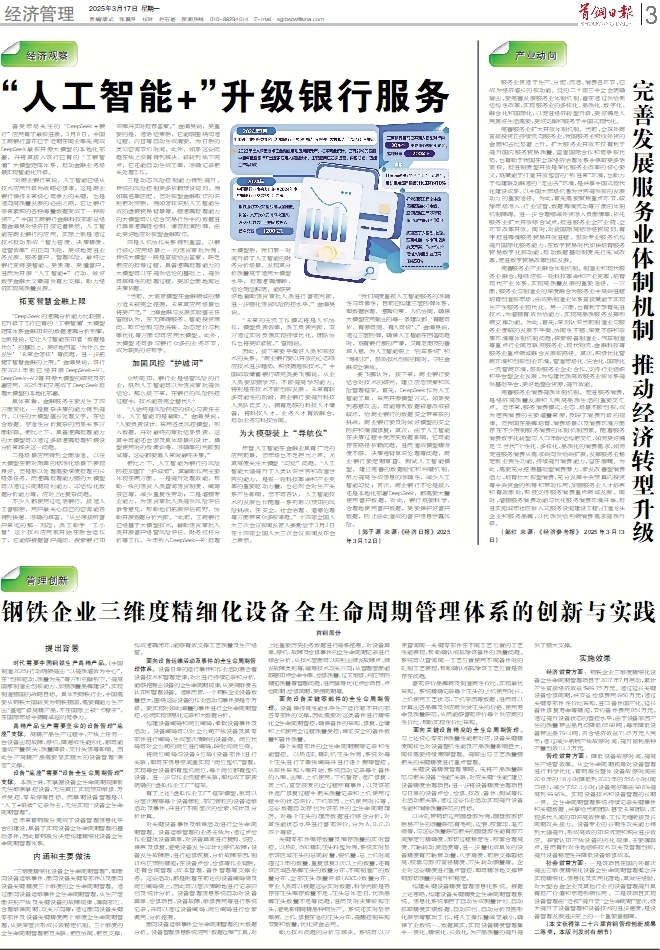
- 返回目录
- 上一篇
- 下一篇
- 放大+
- 缩小-
- 常规
钢铁企业三维度精细化设备全生命周期管理体系的创新与实践
提出背景
时代需要中国钢铁生产高精产品。《中国制造2025》行动纲领提出“以提质增效为中心”,在“创新驱动、质量为先”等方针的指引下,“提高国家制造业创新能力、加强质量品牌建设”,实现制造强国的战略目标。具体到钢铁行业,中国需要从钢铁大国转变为钢铁强国,需要有能力生产出“皇冠”级高精产品,不在国际上被“卡脖子”,在国际市场中拥有卓越的竞争力。
高精产品生产需要坚实的设备管理“底座”支撑。高精产品生产过程中,产线上任何一台设备出现故障、停机、降速或性能劣化,都可能造成产量损失、质量降级、交付失信等影响。因此生产高精产品需要坚实强大的设备管理“底座”支撑。
设备“底座”需要“设备全生命周期管理”支撑。本质上讲,不掌握设备全生命周期规律就无法彻底掌控设备,无法真正实现预知维修、万点受控、零故停等目标。而早期设备管理是以“人工+纸版”记录为主,无法实现“设备全生命周期管理”。
近年来首钢股份完成了设备管理信息化平台的建设,具备了实现设备全生命周期管理的基础条件,因此首钢股份决定构建精细化设备全生命周期管理体系。
内涵和主要做法
“三维度精细化设备全生命周期管理”,即面向设备运维事件、面向设备关键零部件以及面向设备关键精度三个维度的全生命周期管理。通过面向设备运维事件全生命周期管理,从生产层面识别产线及关键设备的故障规律、薄弱部位、合理维保周期、攻关方向等;通过面向设备关键零部件及设备关键精度两个维度全生命周期管理,从更深层次形成长效稳定机制。三个维度的全生命周期管理相互关联、相互协同、相互支撑,构成逻辑闭环,能够有效支撑工艺质量及生产经营。
面向设备运维活动及事件的全生命周期管理体系。设备日常的运行事件和作业活动蕴含着设备技术和管理定律,对之进行持续记录和分析,能够挖掘出设备的全生命周期规律,从更高维度去认知和管理设备。通常而言,一个钢铁企业设备数量巨大,围绕这些设备的作业活动与事件更是千万级。要实现对如此海量的事件进行全生命周期管控,必须实现信息化记录和大数据分析。
构建设备编码和岗位编码,承载设备事件及活动。设备编码可以对全公司产线设备及其零部件进行编码,生成层次清晰的设备树。岗位代码可对全公司的岗位进行编码,映射成岗位树。
将岗位编码与设备9位码(设备部件)进行关联,即可在信息空间里实现“岗位包机”管理,实现每台设备都有包机岗位,每个岗位都有包机设备。进一步与作业流程相关联,即构成了职责明确的“虚拟作业工厂”框架。
有了上述“虚拟作业工厂”框架模型,就可以分层次跟踪每个设备颗粒、部门颗粒的设备运维活动及事件,并进行不同层次的检索、统计及分析计算。
对关键设备事件及维保活动进行全生命周期管理。设备运维管理的业务主线为:通过点检作业查找设备异常,对设备异常进行复测、监控、保养及修复,避免设备发生非计划停机故障;设备发生故障后,进行抢修恢复,分析故障原因,制订纠正预防措施;在设备点检、检修等作业背后,还有合同管理、成本管理、备件管理等支撑业务。这些活动,都是附着在前述的设备编码树及岗位编码树上,因此可以层次清晰地进行记录归档及统计分析。设备管理信息系统自动对设备异常、检修项目、设备故障、维修费用等进行系统记录,并可以通过设备编码、岗位编码进行检索调用、分析挖掘。
面向设备运维事件全生命周期管理的大数据分析。设备管理信息系统应用“数据仓库”工具,对上述重要历史业务数据进行提炼挖掘。对设备异常、停机、故障及检修事件的全生命周期记录进行综合分析,从技术层面可以识别出频发故障点、频发故障类别等,指导技术攻关方向;从管理层面能够感知点检命中率、检修质量、过欠维修、纠正预防措施质量等管理问题,进而指导优化点检项目、点检周期、检修周期、更换周期等。
面向设备关键零部件的全生命周期管理。设备保持高性能水平生产运行离不开内部各零部件的支撑,因此需要对这类备件进行精细化全生命周期管控,确保备件的采购、修复、仓储和上机使用全过程质量受控,保证安全的备件数量和备件质量。
每个关键部件的全生命周期跟踪记录和性能管控。以热连轧精轧机压头为例,系统对每个压头进行了单独编码并进行逐个跟踪管控。从新件采购入库开始,系统自动记录每个备件的入库、出库、上机使用、下机暂存、返厂修复、再上机,直至报废的全过程所有事件,以及该部件返厂修复过程中相关质量记录和上机使用过程中的状态评价、下机原因、上机使用时长等,这些数据自动存档为该部件的全生命周期履历。对每个压头的履历数据进行综合分析,对其性能状态水平进行客观评价,分为A、B、C、D四个等级。
关键零部件库存数量及库存质量的实时管控。以热轧1580精轧压头料包为例,系统实时显示该区域压头的总周转量、装机量、总上机时间超过3年的数量、重复修复3次以上的数量,还有该区域各品牌压头的数量分布、不同制造厂的数量分布、全部压头质量评级(ABCD)数量分布。专业人员可以根据这些实时数据,科学判断是否存在压头库存数量不足、压头总体老旧、优质品牌压头数量不足等问题,进而及时决策新购压头,避免影响高精品种钢生产。系统还实时显示库房、上机、修复在途的压头分布,提醒控制采购节奏和数量,优化资金占用。
助力技术问题的分析与解决。系统可以方便查询同一关键零部件在不同工艺位置的工艺性能表现,帮助确认或排除该备件的质量问题。系统可以查询同一工艺位置使用不同备件时的轧制工艺表现,帮助确认或排除该工艺位置是否存在问题。
客观评价品牌商及制造商性价比,实现最优采购。系统精确记录每个压头的上机使用时长、上机使用工艺状态、下机原因等数据,进而可以计算出各品牌及供应商供货压头的价格、使用寿命及质量缺陷,从而能够客观评价每个供应商的性价比,帮助实现性价比采购。
面向关键设备精度的全生命周期管理。与上述核心零部件质量性能相对应,设备关键精度同样也对设备整机性能及产品质量影响巨大,同样需要持续跟踪管理。提取出与工艺质量强相关的关键精度进行重点管理。
关键设备精度管理策略。先将产品质量缺陷与相关设备“性能”关联,对应关键“性能”建立设备精度治理项目;进一步将设备精度治理项目与日常的设备点检、检修、技改、备件、测试等作业活动相关联,通过这些作业活动实现提升设备性能和消除质量缺陷的目标。
以冷轧带钢切边用圆盘剪为例,圆盘剪剪切后易产生的质量缺陷有毛刺、边浪、胶套印、退刀痕等,与这些质量缺陷相关的圆盘剪性能有剪刀间隙定位精确度、剪切过程稳定性、胶套合理高度、刀轴转动灵活度等,进一步量化成具体的设备精度有刀轴窜动量、八字角度、前后支撑辊标高、胶套与剪刃直径精度、刀头转动惯量等。企业对这些精度进行重点管控,即可精准地支撑带钢剪切质量的提升和稳定。
构建关键设备精度管理信息化系统。根据上述思路,构建设备关键精度全生命周期管理系统。信息化系统承担了自动生成测量计划、自动抓取精度实绩数据、自动归档、自动分析及图形化展示等繁琐工作,将人工操作量减至最小,确保了业数统一、数据真实,实现设备精度管理集中一贯化、精细化、长效化,为产品质量的提升提供了强大支撑。
实施效果
经济效益方面:钢铁企业三维度精细化设备全生命周期管理项目于2017年7月启动,累计产生直接经济效益5989.75万元。通过延长关键设备检修周期,共节省检修费用4950万元;通过关键零部件性价比采购,进口备件国产化,延长备件修复寿命等措施,节约备件费用854万元。通过提升设备状态的管控水平,由于设备原因产生的质量带出品月均降低65.98吨,每年降低设备带出品791.4吨,折合经济效益71.45万元人民币;通过减少瓶颈产线故停时间,提升盈利品种产量创效114.3万元。
管理效益方面:降低设备故停时间,提高生产经营效率。从全生命周期视角对设备管理进行科学优化,首钢股份整体设备故停时间由2018年的118小时降低到2023年的55.6小时(同口径),减少了62.4小时;设备完好率由98.6%提高到99.96%。实现设备技术和设备管理的长期一贯。全生命周期管理系统持续记录关键事件和关键数据,共享给当前团队甚至未来团队,实现多代人间的知识高效传承、工作无缝衔接及长周期攻关接力。设备专业的长期性攻关能力得到大幅提升,形成高效的知识沉淀和积分进步效应。探索认知产线设备的劣化规律、主要薄弱点,进而有针对性地组织技术攻关及管理创新,提升设备稳定性并降低设备维修成本。
社会效益方面:一是该项目在国内外首次提出三维度精细化设备全生命周期管理概念并实现精细化、信息化及实用化落地,其做法经验,对大型冶金企业及其他行业的设备管理提升具有推广价值和示范引领作用。二是该项目实现设备管理由“近视”提升至“全生命周期”层次,极大提升了设备管理和设备技术的进步速度,是设备管理发展进步史上的一个重要里程碑。(本文获得第二十六届首钢管理创新成果二等奖,本版刊发时有删节)