分享到微信朋友圈x
打开微信,点击底部的“发现”,
使用“扫一扫”即可将网页分享至朋友圈。
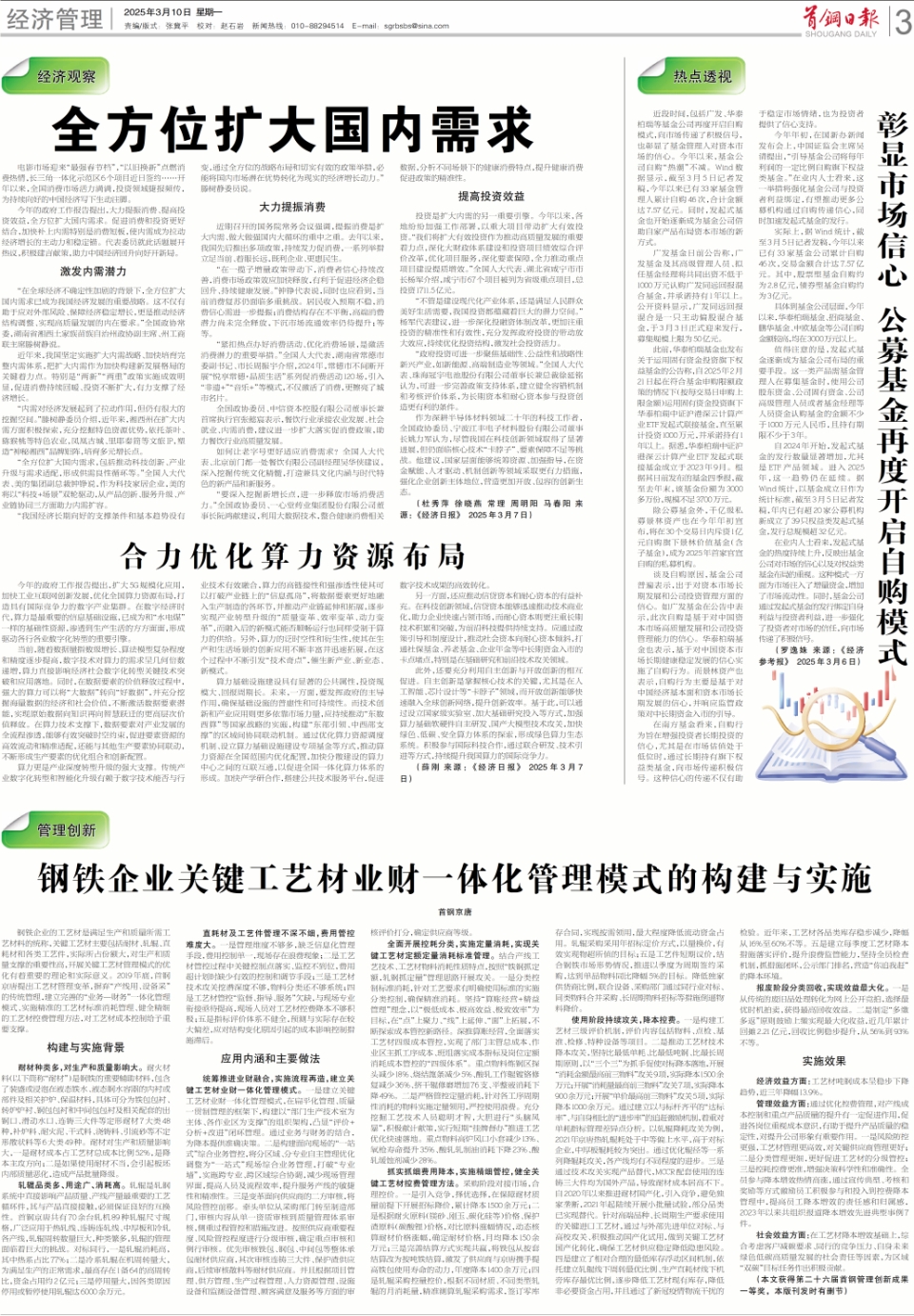
- 返回目录
- 上一篇
- 下一篇
- 放大+
- 缩小-
- 常规
钢铁企业关键工艺材业财一体化管理模式的构建与实施
钢铁企业的工艺材是满足生产和质量所需工艺材料的统称,关键工艺材主要包括耐材、轧辊、直耗材和各类工艺件,实际所占份额大,对生产和质量支撑的重要性高,开展关键工艺材管理模式的优化有着重要的理论和实际意义。2019年底,首钢京唐提出工艺材管理变革,摒弃“产线用、设备采”的传统管理,建立完善的“业务—财务”一体化管理模式、实施精准的工艺材标准消耗管理、健全精细的工艺材控费管理方法,对工艺材成本控制给予重要支撑。
构建与实施背景
耐材种类多,对生产和质量影响大。耐火材料(以下简称“耐材”)是钢铁的重要辅助材料,包含了装盛或浸泡在液态铁水、液态钢水容器的内衬或部件及相关护炉、保温材料,具体可分为铁包包衬、转炉炉衬、钢包包衬和中间包包衬及相关配套的出钢口、滑动水口、连铸三大件等定形耐材7大类48种,补炉料、耐火泥、干式料、浇铸料、引流砂等不定形散状料等6大类49种。耐材对生产和质量影响大,一是耐材成本占工艺材总成本比例52%,是降本主攻方向;二是如果使用耐材不当,会引起板坯内部质量恶化,造成产品批量降级。
轧辊品类多、用途广、消耗高。轧辊是轧钢系统中直接影响产品质量、产线产量最重要的工艺循环件,其与产品直接接触,必须保证良好的互换性。首钢京唐共有70余台轧机89种轧辊尺寸规格,广泛应用于热轧线、连铸连轧线、中厚板和冷轧各产线,轧辊周转数量巨大,种类繁多,轧辊的管理面临着巨大的挑战。对标同行,一是轧辊消耗高,其中热系占比77%;二是冷系轧辊在机周转量大,为满足生产的正常需求,最高存在1备64的高周转比,资金占用约2亿元;三是停用量大,因各类原因停用或暂停使用轧辊达6000余万元。
直耗材及工艺件管理不深不细,费用管控难度大。一是管理维度不够多,缺乏信息化管理手段,费用控制单一,现场存在浪费现象;二是工艺材管控过程中关键控制点落实、监控不到位,费用超计划时缺少有效的控制和调节手段;三是工艺材技术攻关挖潜深度不够,物料分类还不够系统;四是工艺材管控“监督、指导、服务”欠缺,与现场专业衔接亟待提高,现场人员对工艺材控费降本不够积极;五是指标评价体系不健全,预测与实际存在较大偏差,应对结构变化原因引起的成本影响控制措施滞后。
应用内涵和主要做法
统筹推进业财融合,实施流程再造,建立关键工艺材业财一体化管理模式。一是建立关键工艺材业财一体化管理模式,在扁平化管理、质量一贯制管理的框架下,构建以“部门生产技术室为主体、各作业区为支撑”的组织架构,凸显“评价+分析+改进”闭环管理。通过业务与财务的结合,为降本提供准确决策。二是构建面向现场的“一站式”综合业务管控,将分区域、分专业自主管理优化调整为“一站式”现场综合业务管理,打破“专业墙”,实施跨专业、跨区域综合协调,减少现场管理界面,提高人员及流程效率,提升服务产线的敏捷性和精准性。三是变革面向供应商的二方审核,将风险管控前移。牵头单位从采购部门转至制造部门,审核内容从单一资质审核到质量管理体系审核,侧重过程管控和措施改进。按照供应商重要程度、风险管控程度进行分级审核,确定重点审核和例行审核。优先审核铁包、钢包、中间包等整体承包耐材供应商,其次审核连铸三大件、保护渣供应商,后续审核散料等耐材供应商。并且根据项目管理、供方管理、生产过程管理、人力资源管理、设施设备和监测设备管理、顾客满意及服务等方面的审核评价打分,确定供应商等级。
全面开展控耗分类,实施定量消耗,实现关键工艺材定额定量消耗标准管理。结合产线工艺技术、工艺材物料消耗性质特点,按照“铁钢抓定额,轧钢抓定量”管理思路开展攻关。一是分类控制标准消耗,针对工艺要求有明确使用标准的实施分类控制,确保精准消耗。坚持“算账经营+精益管理”理念,以“极低成本、极高效益、极致效率”为目标,在“点”上聚力、“线”上延伸、“面”上拓展,不断探索成本管控新路径。深推算账经营,全面落实工艺材四级成本管控,实现了部门主管总成本、作业区主抓工序成本、班组落实成本指标及岗位定额消耗成本管控的“四级体系”。重点物料炼钢区探头减少18%、烧结篦条减少5%、酸轧工作辊镀铬修复减少36%、挤干辊修磨增加76支、平整液消耗下降49%。二是严格管控定量消耗,针对各工序周期性消耗的物料实施定量领用,严控使用浪费。充分挖掘工艺技术人员聪明才智,大胆进行“头脑风暴”,积极献计献策,实行短期“挂牌督办”推进工艺优化快速落地。重点物料高炉风口小套减少13%、氧枪寿命提升35%、酸轧轧制油消耗下降23%、酸轧缓蚀剂减少28%。
抓实抓细费用降本,实施精细管控,健全关键工艺材控费管理方法。采购阶段对接市场,合理控价。一是引入竞争,择优选择,在保障耐材质量前提下开展招标降价,累计降本1500余万元;二是根据耐火原料(镁砂、刚玉、碳化硅等)价格、保护渣原料(碳酸锂)价格,对比原料涨幅情况,动态核算耐材价格涨幅,确定耐材价格,月均降本150余万元;三是完善结算方式实现共赢,将铁包从按套结算改为按吨铁结算,激发了供应商与京唐携手提高铁包使用寿命的动力,年度降本1400余万元;四是轧辊采购控量控价,根据不同材质、不同类型轧辊的月消耗量,精准测算轧辊采购需求,签订零库存合同,实现按需领用,最大程度降低流动资金占用。轧辊采购采用年招标定价方式,以量换价,有效实现物超所值的目标;五是工艺件短期议价,结合钢铁市场形势情况,推进以季度为周期签约采购,达到单品物料同比降幅5%的目标。降低独家供货商比例,联合设备、采购部门通过同行业对标、同类物料合并采购、长周期物料招标等措施倒逼物料降价。
使用阶段持续攻关,降本控费。一是构建工艺材三级评价机制,评价内容包括物料、点检、基准、检修、特种设备等项目。二是推动工艺材技术降本攻关,坚持比最低单耗、比最低吨钢、比最长周期原则,以“三个三”为抓手促使对标降本落地,开展“消耗金额最高前三物料”攻关9项,实际降本1500余万元;开展“消耗量最高前三物料”攻关7项,实际降本900余万元;开展“单价最高前三物料”攻关5项,实际降本1000余万元。通过建立以与标杆齐平的“达标率”、与自身相比的“进步率”的追赶激励机制,着重对单耗指标管理差异点分析。以轧辊降耗攻关为例,2021年京唐热轧辊耗处于中等偏上水平,高于对标企业,中厚板辊耗较为突出。通过优化辊径等一系列降辊耗攻关,各产线均有不同程度的进步。三是通过技术攻关实现产品替代,MCCR配套使用的连铸三大件均为国外产品,导致耐材成本居高不下。自2020年以来推进耐材国产化,引入竞争,避免独家垄断,2021年起陆续开展小批量试验,部分品类已实现替代。针对高端品种、长周期生产要求使用的关键进口工艺材,通过与外部先进单位对标、与高校攻关、积极推动国产化试用,做到关键工艺材国产化转化,确保工艺材供应稳定降低隐患风险。四是建立了相对合理的最低库存浮动区间机制,依托建立轧辊线下周转最优比例、生产直耗材线下机旁库存最优比例,逐步降低工艺材现有库存,降低非必要资金占用,并且通过了新冠疫情物流干扰的检验。近年来,工艺材各品类库存稳步减少,降幅从16%至60%不等。五是建立每季度工艺材降本措施落实评价,提升浪费监管能力,坚持全员检查机制,抓措施闭环,公示部门排名,营造“你追我赶”的降本环境。
报废阶段分类回收,实现效益最大化。一是从传统的废旧品处理转化为网上公开竞拍,选择最优时机拍卖,获得最高回收效益。二是制定“多缴多返”原则鼓励上缴实现最大化收益,近几年累计回摊2.21亿元,回收比例稳步提升,从56%到93%不等。
实施效果
经济效益方面:工艺材吨钢成本呈稳步下降趋势,近三年降幅13.9%。
管理效益方面:通过优化控费管理,对产线成本控制和重点产品质量的提升有一定促进作用,促进各岗位重视成本意识,有助于提升产品质量的稳定性,对提升公司形象有重要作用。一是风险防控更强,工艺材管理更高效,对关键供应商管理更好;二是分类管理更细,更好促进工艺材的分级管控;三是控耗控费更准,增强决策科学性和准确性。全员参与降本增效热情高涨,通过宣传典型、考核和奖励等方式激励员工积极参与和投入到控费降本管理中,提高员工降本增效的责任感和归属感,2023年以来共组织报道降本增效先进典型事例7件。
社会效益方面:在工艺材降本增效基础上,综合考虑客户减碳要求、同行的竞争压力、自身未来绿色低碳高质量发展的社会责任等因素,为区域“双碳”目标任务作出积极贡献。(本文获得第二十六届首钢管理创新成果一等奖,本版刊发时有删节)