分享到微信朋友圈x
打开微信,点击底部的“发现”,
使用“扫一扫”即可将网页分享至朋友圈。
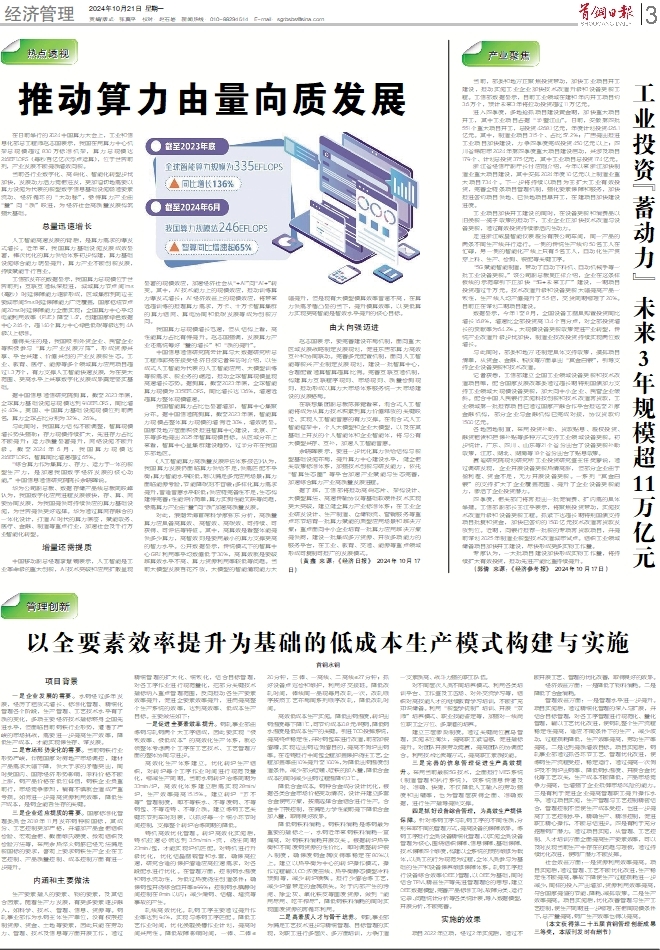
- 返回目录
- 上一篇
- 下一篇
- 放大+
- 缩小-
- 常规
以全要素效率提升为基础的低成本生产模式构建与实施
项目背景
一是企业发展的需要。水钢经过多年发展,经历了粗放式增长、标准化管理、精细化管理各个阶段,生产管理、工艺技术水平有了质的变化,多项主要经济技术指标跻身全国先进水平,但面临目前钢铁行业形势,遭遇了严峻的市场挑战,需要进一步提高生产效率,降低生产成本,才能实现保生存、谋发展。
二是市场形势变化的需要。当前钢铁行业形势严峻,伴随国家对房地产市场调控,建材产品需求大幅下降,供大于求的矛盾突出,同时受国内、国际经济形势影响,原料价格不断上涨,钢产品价格在低位徘徊,钢铁企业负重前行,市场竞争激烈,稍有不慎就会造成严重亏损。如何进一步提高资源利用效率,降低生产成本,是钢企能否生存的关键。
三是企业适应提质的需要。国家标准化管理委员会2018年11月发布钢种新国标,其成份、工艺控制更加严格,并增加产品金相组织检验、宏观金相、截面维氏硬度、微观组织及检验方法等,采用余热淬火钢筋已经无法满足新国标的要求,客观上要求钢铁生产企业在工艺控制、产品质量控制、成本控制方面有进一步提升。
内涵和主要做法
生产要素指人的要素、物的要素,及其结合因素。随着生产力发展,有更多要素逐步融入,如科学、技术、管理、信息、资源等。钢轧事业部作为水钢主体生产单位,没有权限控制资源、资金、土地等要素,因此只能在劳动力、管理、技术及信息等方面开展工作,通过精细管理的扩大化、细致化,结合目标管理,对各工序作业进行规范量化,把部分关键技术指标纳入重点管理范围,反向推动各生产要素效率提升,促进全要素效率提升,进而提高整个生产系统的效率,达到高效率、低成本生产目标。主要做法如下:
一是促进全要素效率提升。钢轧事业部由炼钢与轧钢两个大工序组成,因此要实现“极致效率、极低成本”的高效化生产体系,就必须整体考虑两个工序在工艺技术、工艺管理方面的整体协同与进步。
高效化生产体系建立。优化转炉生产组织,对转炉每个工序作业时间进行规范及量化,缩减生产周期。当前水钢转炉冶炼周期为33min/炉,高效化体系建立后需实现28min/炉,生产效率提高15.15%。建立转炉“五不等”管理制度,即不等铁水、不等废钢、不等钢包、不等连铸、不等介质。建立炼钢工艺关键环节列车时刻表,以抓好每一个细小环节时间控制,支撑整个转炉冶炼周期的降低。
铸机高效优化管理。转炉高效化实施后,铸机拉速必须达到3.5m/min·流,浇注周期23min/包,才能实现炉机匹配。对铸机进行升级优化,优化结晶器铜管和水套,确保高拉速,研究合适的保护渣适应高拉速需求,对各段配水进行优化。在管理方面,控制钢水温度和钢水流动性,为低过热度浇注创造条件;确保钢包开浇综合自开率≥99%;控制钢水镇静时间控制在8min以内;减少漏钢、结瘤、堵流等事故的产生。
轧线高效优化。轧钢工序主要通过提升作业率达到94%,实现与炼钢工序匹配。降低工艺作业时间,优化换辊换槽作业计划,提高时间共用性。降低故障影响时间,一棒、二棒≤20分钟,三棒、一高线、二高线≤27分钟;抓好设备点巡检和维护,利用好交接班。降低改轧时间,棒线同一品规每月改轧一次,改轧顺序按照工艺布局同系列顺序改轧,降低改轧时间。
高效低成本生产实施。降低出钢温度,转炉出钢温度每下降1℃,可节约成本0.8元/吨钢,降低钢水温度是低成本生产的关键。引进TCO投弹系统,提高终点稳定性,并对钢包车进行改造,前部加装渣罐,实现边出钢边倒渣目的,提高不倒炉出钢率。在连铸推行中间包全程加盖保护浇注工艺,全程加盖率由10%提升至100%,为降低出钢温度创造条件。减少部分硅锰、硅铁的加入量,降低合金成本的同时减少出钢过程温降约3℃。
降低合金成本。钢种合金成分设计优化,根据各类合金市场价格变动情况,设计并建立多套合金使用方案,按需选择合金组合进行生产。合金中下限控制,在满足力学性能前提下降低合金加入量,取得良好效果。
降低钢铁料消耗。钢铁料消耗是炼钢最为重要的指标之一,水钢近年来钢铁料消耗一直偏高,对钢铁料消耗开展攻关。根据转炉热平衡和不同废钢资源的性价比,即时调整转炉装入制度,确保废钢金属收得率稳定在80%以上。建立以热平衡为中心的转炉操作模式,操作过程辅以CO浓度曲线、热平衡静态模型冷料预测等,减少转炉喷溅。推行少渣冶炼工艺,减少炉渣带走的金属损失。对于内部产生的污泥、除尘灰、氧化铁皮等固废资源,做到“能用尽用、吃干榨尽”,降低钢铁料消耗的同时实现固废资源的再循环利用。
二是高素质人才与骨干培养。钢轧事业部为满足工艺技术进步与精细管理、目标管理的实现,对职工进行多层次、多方面培训,力争打造一支素质高、战斗力强的职工队伍。
对不同层次人员不同培养模式、利用各类培训平台、工作室及工匠场、对外交流学习等,组织对高技能人才的继续教育学习培训,不断扩充知识储备。利用“新型学徒制”培训、开展“双师”培养模式、职业技能鉴定等,加强对一线岗位职工全方位、多渠道的培养。
建立三层激励制度。通过关键岗位赛马管理,实施末位淘汰,提高职工紧迫感,促进指标提升。对团队开展劳动竞赛,提高团队的协调配合。利用技术比武等方式,提高职工素质技能。
三是完善的信息管理促进生产高效提升。采用当前最新5G技术,全面推行MES系统(制造管理和执行系统),该系统信息传递及时、准确、快捷,不仅降低人工输入的劳动强度和出错率,也为管理层获得全面、准确数据,进行生产指导提供支撑。
四是抓好设备综合管理,为高效生产提供保障。针对炼钢工序与轧钢工序的不同性质,分别采取不同的管理方式,提高设备的保障效果。炼钢工序推行全员设备精细化管理,以实施全员设备管理为核心,围绕组织保障、信息保障、基础保障、技术保障四个维度,构建以全系统的预防维修为载体,以员工的行为规范为过程,全体人员参与为基础的生产和设备保养维修保障体系。轧钢工序推行设备综合效率(OEE)管理,以OEE为基础,同时结合TPM、精益生产等先进管理理论的思想,建立OEE数据模型,完善产品标准工时、故障分类、运行记录、问题统计分析等各类统计表,导入数据模型,开展分析,不断完善。
实施的效果
项目2022年立项,经过2年实施后,通过不断开展工艺、管理的优化改善,取得良好的效果。
经济效益方面:一是降低了物料消耗。二是降低了合金消耗。
管理效益方面:一是管理水平进一步提升。项目实施后,通过精细化管理的深入与扩展,并结合目标管理,对各工序管理进行规范化、量化管理,辅以工艺优化改进,使钢轧整个生产流程稳定性提高,适应不同条件下的生产,减少波动,过程损耗降低,生产效率提高,劳动生产率提高。二是达到提质增效目标。项目实施后,钢轧事业部通过抓各环节工艺、管理优化改进,使炼钢生产流程受控,稳定运行,通过提高一次倒炉及不倒炉出钢率、降低钢水温度、开展合金优化等工艺攻关,生产成本不断降低,产品市场竞争力提高,也增强了企业抵御市场风险的能力。三是有利于促进企业提高管理职工提升操作水平。通过项目实施,生产管理与工艺控制精密结合,管理控制不但使生产成本受控,也进一步提高了工艺控制水平,精确生产、精准控制,促进职工精心操作,不断总结进步。四是有利于充分挖掘钢厂潜力。通过项目实施,从管理、工艺控制、人才培训方面全面提高生产要素效率,可以及时发现当前生产中存在的问题与短板,通过持续优化改进,使钢厂潜力不断发挥。
社会效益方面:一是资源利用效率提高。项目实施后,通过管理、工艺不断优化改进,生产稳定性不断提高,事故下降使生产过程损耗进一步减少,同样的投入产出增加,资源利用效率提高,符合国家提倡的节能、降耗、减排政策。二是生产效率提高。项目实施后,优化改善管理与生产工艺控制,使生产周期进一步缩短,在相同规模条件下,总产量提高,钢厂生产效率也得以提高。(本文获得第二十五届首钢管理创新成果三等奖,本版刊发时有删节)