分享到微信朋友圈x
打开微信,点击底部的“发现”,
使用“扫一扫”即可将网页分享至朋友圈。
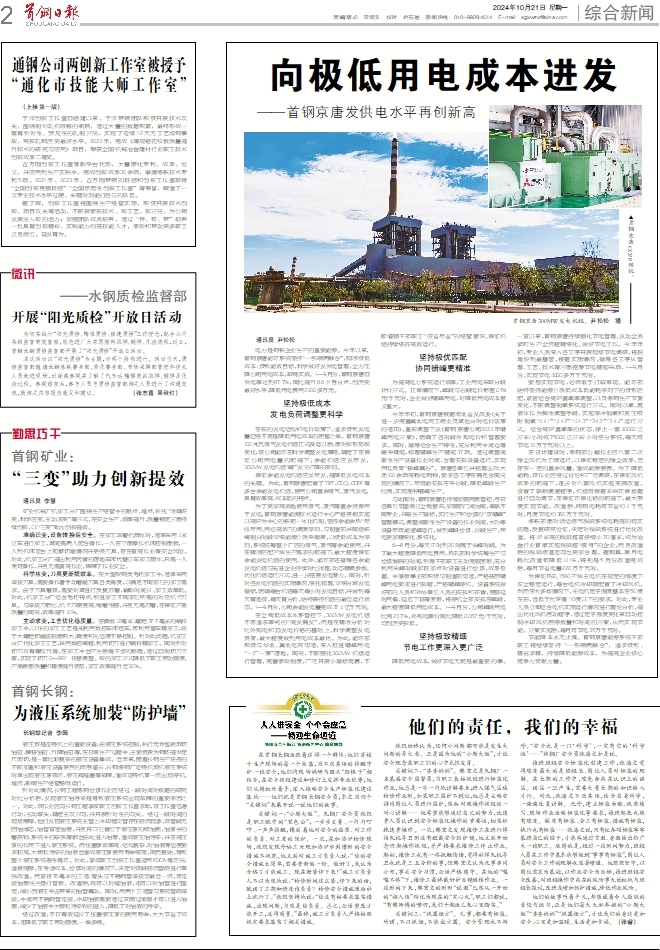
- 返回目录
- 上一篇
- 下一篇
- 放大+
- 缩小-
- 常规
向极低用电成本进发
——首钢京唐发供电水平再创新高
![]() |
首钢京唐CCPP燃机。 |
![]() |
首钢京唐300MW发电机组。 |
电力是钢铁企业生产的重要能源。今年以来,首钢京唐能环系统坚持“一引领两融合”,瞄准极低成本、极致能效目标,科学做好发供电管理,全力压降公司用电成本,取得实效。1—9月份,首钢京唐自供电率达到87.7%,同比提升6.6个百分点,创历史最好水平,降低用电费用2400多万元。
坚持极低成本
发电负荷调整更科学
在新的发电结构和电价政策下,追求极致发电量已经不再是降低用电成本的明智之举。首钢京唐100兆瓦煤气发电机组正式投运以后,面对新形势新变化,该公司能环部科学调整发电策略,确定了在保证公司用电量的前提下,余能机组应发尽发,300MW发电机组“峰”发“谷”降的原则。
保证余能发电机组应发尽发,是降低发电成本的关键。为此,首钢京唐配置了TRT、CDQ、CCPP等多台余能发电机组,使用公司富余煤气、蒸汽发电,具有效率高、成本低的特点。
为了更加高效地使用煤气、蒸汽等富余资源用于发电,首钢京唐能源技术运行中心严格贯彻实施以高炉为中心的铁前一体化机制,坚持余能余热“尽收尽用、用必高效”的调度原则,与制造部共同组织编制分时段详细能源介质平衡表,以极低成本为原则,系统统筹整个厂区的煤气、蒸汽等余能使用,并在精准匹配产线生产需求的前提下,最大程度保证余能发电机组的使用。此外,能环部还指导各余能发电机组与先进企业持续对比找差,动态精调参数、优化机组运行方式,进一步挖掘发电潜力。同时,针对各发电机组的实际情况,细化梳理、详细分解发电指标,明确每台机组每天每小时发电目标,并做到每天有通报、每天有分析,始终保持机组的最佳运行状态。1—9月份,公司余能发电量完成37.4亿千瓦时。
在全局低成本体系管控下,300MW发电机组不再追求单纯的“高发满发”,而是在精准分析对比外购电和自发电价格的基础上,科学调整发电负荷,最大程度做到用电成本最优。为此,能环部积极与华北、冀北电网沟通,深入推进错峰用电“一厂一策”落地。同时,不断强化300MW机组运行管理,完善激励制度,广泛开展小指标竞赛,不断增强干部职工“应省尽省”的经营意识,保证机组持续经济高效运行。
坚持极优匹配
协同错峰更精准
为提高电力系统运行效率,工业用电采取分段计价方式。正常情况下,峰段与谷段电价相差0.59元/千瓦时,企业做好错峰用电,对降低用电成本意义重大。
今年年初,首钢京唐根据河北省发改委《关于进一步完善冀北电网工商业及其他分时电价政策的通知》,重新调整下发《首钢京唐公司2024年错峰用电方案》,明确了各时段外购电价和管理要求。同时,指导结合生产特性,充分利用中间仓等缓冲措施,梳理错峰生产措施37项。通过调整间歇性生产设备作业时间、合理安排设备运行,实现用电负荷“移峰填谷”。京唐各单位共梳理出26大类100余项高耗电钢种,要求各工序在满足合同兑现的情况下,尽可能安排在平谷段,降低峰段生产比例,实现品种错峰生产。
与此同时,首钢京唐还持续加强界面管控,号召各单位牢固树立全局意识,加强部门间协同,串联不同专业,并联生产指标,实行生产和检修的“双错峰”管理模式,调整间歇性生产设备的作业时间,大功率设备尽可能避峰运行,做到峰段检修、谷段生产,用电更加精细化、系统化。
6—8月份,每天17时到20时属于尖峰时段。为了最大程度降低用电费用,热轧部科学统筹生产与检修消缺的时间,引导干部职工主动克服困难,充分利用尖峰时段加班加点对设备进行检修,成果显著。中厚板事业部积极与制造部沟通,严格按照错峰用电要求进行排程,严格错峰停机。设备系统做好部内人员和外协单位人员的安排和布置,克服延时用餐、延迟下班等困难,将停机全部安排在峰段,最大程度降低用电成本。1—9月份,公司峰段用电比例23.7%,外购电单价同比降低0.067元/千瓦时,均创历史新低。
坚持极致精细
节电工作更深入更广泛
降低用电成本,做好节电无疑是最重要的事。一直以来,首钢京唐持续强化节电管理,发动全员紧盯生产全流程精细化,做好节电工作。今年年初,专业人员深入各工序开展现场节电调研,将触角伸到最基层,根据实际情况,指导各工序从管理、工艺、技术等方面挖潜节电措施99项,1—9月份,实现节电4000多万千瓦时。
要想实现节电,必须敢于打破常规。能环部始终坚持能源介质低成本低能耗原则下的极致匹配,紧密结合高炉富氧率调整,以及炼钢生产节奏变化,不断调整制氧系统运行方式。同时以氧、氮液体作为弹性调整手段,实施深冷制氧和变压吸附制氧“4+1”“4+2”“4+3”“3+3”“3+4”运行方式。结合高炉富氧率的状态,停止一套40000立方米/小时或75000立方米/小时空分系统,每天可节电10万千瓦时以上。
在设计建设时,炼钢部公辅作业区八套二次除尘风机为工频运行,以保证稳定的除尘效果,但存在一定的富余风量,造成能源浪费。为了降低能耗,该作业区经过讨论和广泛调研,在保证风机效果的前提下,逐步对八套风机实施变频改造。设置了联锁调速程序,机组可根据末端环保数据进行自动调节,在保证环保达标的前提下,最大限度实现节能。改造后,吨钢电耗可节省约4千瓦时,月度节电约360万千瓦时。
炼铁部面对烧结烟气脱硫系统电耗高的现实问题,反复研究论证,决定对脱硫系统进行优化改造。将45米高的脱硫塔直径缩小70厘米,成为冶金行业首家实施脱硫塔“瘦身”的企业,而且改造后的脱硫烟道走向也更加合理。据测算,单月电耗比改造前降低14.1%,特别是5月份改造完成后,每月节省电量220万千瓦时。
为保证热轧1580产线主电机在规定的温度下安全稳定运行,每台电机冷却器配置了冷却风机。然而在大多数情况下,主电机定子温度基本在50度左右,远低于允许值110度以下的要求。对此,专业人员立即结合电机实际运行情况进行理论分析,提出优化风机启动程序,通过定子温度变化来自动控制冷却风机启停数量和时间的方案,从而实现节能。方案实施后,每月可节电35万千瓦时。
节能降本永无止境。首钢京唐能源系统干部职工将继续坚持“一引领两融合”,追求极致、精益求精,持续降低能源成本,为提高企业核心竞争力贡献力量。