分享到微信朋友圈x
打开微信,点击底部的“发现”,
使用“扫一扫”即可将网页分享至朋友圈。
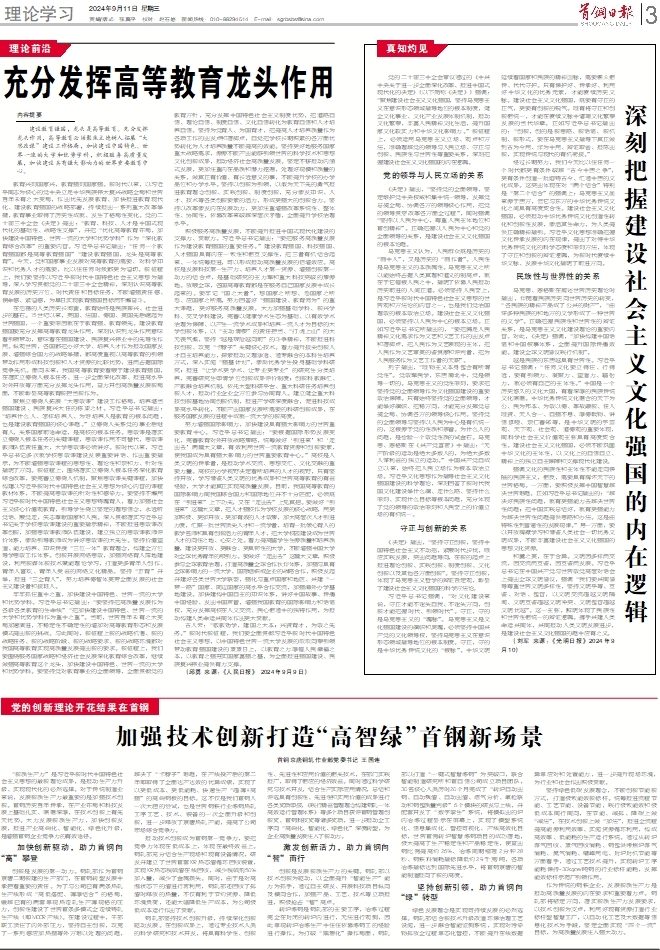
- 返回目录
- 上一篇
- 下一篇
- 放大+
- 缩小-
- 常规
加强技术创新打造“高智绿”首钢新场景
“新质生产力”是习近平新时代中国特色社会主义思想的最新理论成果,是推动生产力升级、实现现代化的必然选择。对于传统制造业来说,发展新质生产力最重要的是加强技术创新。首钢历史百年传承,在产业布局和科技发展上基础扎实、底蕴深厚,在技术创新上有先天优势。大力发展新质生产力,加快创新发展,推进产业高端化、智能化、绿色化升级,是增强首钢企业竞争力的有效途径。
加快创新驱动,助力首钢向“高”攀登
创新是发展的第一动力。钢轧部作为首钢京唐二期新建的生产部门,在首钢转型发展中承担着重要的责任。为了与公司已有两条热轧生产线形成“高低搭配、薄厚结合”的格局,缓解已有的两套常规热连轧生产薄规格的压力,创新性建设了世界首条多模式全连续铸轧生产线(即MCCR产线)。在建设过程中,干部职工顶住了内外部压力,坚持自主创新,攻克了一系列感应加热器等外方难以处理的问题,解决了“卡脖子”难题,在产线投产后的第二年即取得了全面达产达效的优异成绩,实现了以更低成本、更低能耗、快速生产“超薄+高强”的高端钢板的目标。这不仅是我们首钢人一次大胆的尝试,也是世界钢铁行业炼钢热轧工序工艺、技术、装备的一次全面升级和创新,进一步释放了京唐热轧产能,提高了公司市场综合竞争力。
推动技术创新成为首钢第一竞争力,要把竞争力体现在低成本上,体现在最终效益上。钢轧部充分结合生产现场和现有设备情况,研发并建立了世界首套KR热态渣循环回收装置,实现KR热态脱硫渣在线回收,减少脱硫剂50%加入量,减少了金属损失。同时,由于是对高温状态下的渣进行再利用,钢轧部还回收了排渣时释放的热量,不仅有利于节约资源、降低环境负荷,还能大幅降低生产成本,为公司极低成本运行作出了贡献。
钢轧部坚持技术创新升级,持续深化创新驱动发展。在创新成果上,通过专业技术人员的科学研究和技术开发,将具有科学性、创新性、先进性和应用价值的相关技术,在部门实践推广,取得了相应的经济效益。同时通过科学研究与技术开发,结合生产实际应用情况,总结和评选具有创新性、先进性和实用价值的成果进行各类奖项申报,《践行精益管理理念构建钢轧一体高效运行管理体系》等多个项目获评首钢管理创新奖、首钢科技奖等诸多奖项,进一步推动全工序向“高端化、智能化、绿色化”深度转型,为企业高质量发展注入了新动力。
激发创新活力,助力首钢向“智”而行
创新是发展新质生产力的关键。钢轧部以技术创新为驱动,以全面提升“智能生产”能力为抓手,通过自主研发、开展科技项目纵向及横向合作,加强产品、工艺、技术等立项推进,积极抢占“智”高点。
转炉炼钢是钢轧部的主要工序,冶炼过程完全在封闭的转炉内进行,无法进行观测,因此常规转炉冶炼生产中往往依靠炼钢工的经验进行操作。为打破“黑箱化”操作局面,钢轧部以打造“一键式智慧炼钢”为突破口,联合智能制造研究所和首自信公司成立项目团队,30名核心人员历时20个月完成了“转炉自动出钢、自动溅渣、自动出渣、烟气分析、氧枪联动和钢包质量判级”6个模块的研发与上线,并配套开发了“数字孪生”系统,将模拟出的炉内冶炼过程显示在屏幕上,实现了模型系统化、信息集成化、管控可视化、产线高效化目标,世界首例转炉智慧炼钢项目的成功落地,极大提高了生产稳定性和产品稳定性,使直出钢比例提高约26%、冶炼周期缩短2分钟28秒、钢铁料消耗指标降低约2.9千克/吨,各项冶炼指标达到国际先进水平,将首钢京唐的智能制造推向了新的高度。
坚持创新引领,助力首钢向“绿”转型
绿色发展理念是实现可持续发展的必然选择。钢轧部结合新技术升级改造环保治理工艺设施,进一步融合智能监测系统,实现对污染物排放全过程常态化管控,不断提升在线数据异常应对和处置能力,进一步提升现场环境,为行业和社会作出积极贡献。
坚持绿色低碳发展理念,不断创新节能新方式,打造极致能效新标杆。统筹推进流程节能、工艺节能、设备节能,践行极致能效和极低成本同行同向,在节能、减排、降碳上做“减法”,在技术创新上做“加法”,推进全流程提高能源利用效率、实施资源循环利用,构成高效率、低能耗的生产运行系统。通过从转炉煤气回收、蒸汽回收消耗、钢包烘烤焦炉煤气消耗、氮气消耗、错峰用电、封炉封机节能等方面着手,通过工艺技术提升,实现转炉工序能耗保持-30kgce/吨钢的行业标杆能耗,发挥能效标杆示范厂引领作用。
作为传统的钢铁企业,发展新质生产力是推动高质量发展的内在要求和重要着力点。钢轧部将锚定方向,落实新质生产力发展要求,以技术创新为支点,利用好现有资源打造行业标杆型智慧工厂,以自动化工艺及大数据等信息化技术为手段,坚定全面实现“四个一流”目标,为高质量发展注入强大动力。